製造工程
製造工程
本社工場
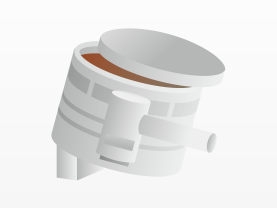
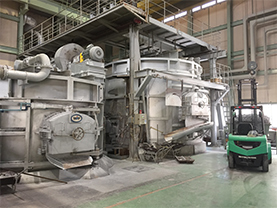
1溶解
最大1200℃の炉の中で15トン以上のアルミを溶かして成分を調整します。

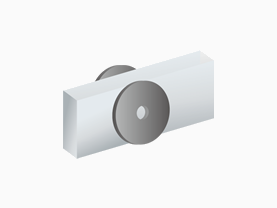
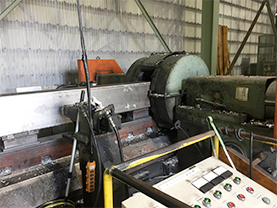
3面削
酸化被膜を削り取るため、両面を削る面削が行われます。

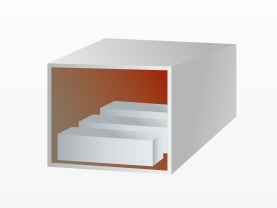
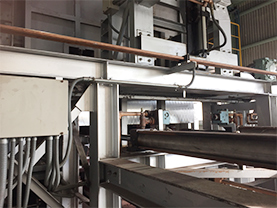
4均熱
熱間圧延を行う前に、440~610℃で均熱処理を行います。

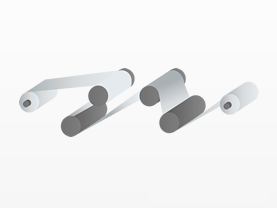

7テンションレベラーライン
圧延したアルミニウム板の歪みを矯正し、高精度に仕上げます。

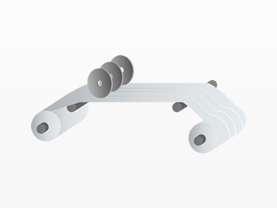
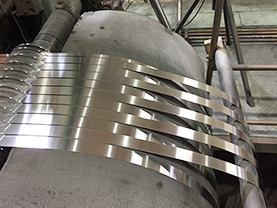
8スリッターライン
指定のサイズにコイルの幅を切断しながら巻き取ります。

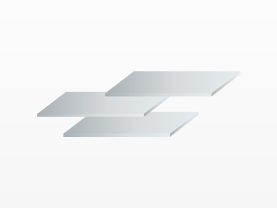
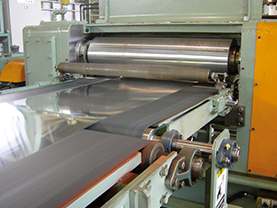
9シャーライン
板の長さと幅を指定のサイズに切断します。

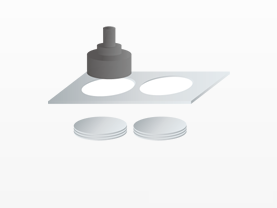
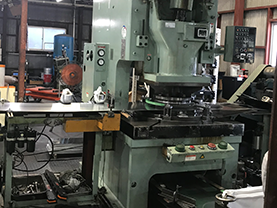
10プレス
コイルから色々なサイズの金型で丸板を抜き取ります。

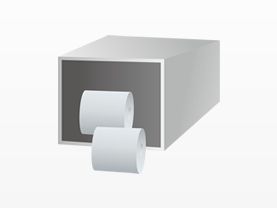
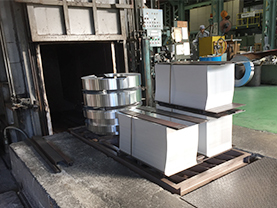
11焼鈍
焼鈍は材料の軟化と残留応力の除去のために行います。

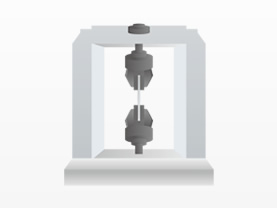
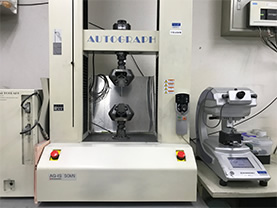
12検査
梱包前に寸法・機械的性質(材料強度)を計ります。

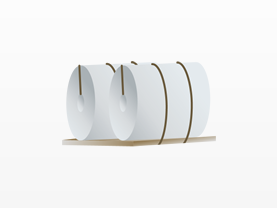
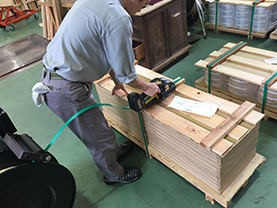
13梱包
完成した製品を検品・梱包し、出荷します。
大山工場
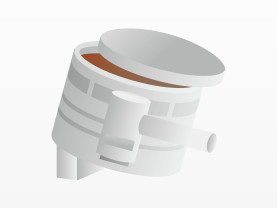
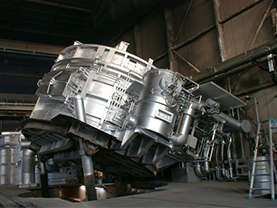
1溶解
最大1200℃の炉の中で20トン以上のアルミを溶かして成分を調整します。

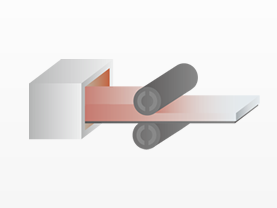
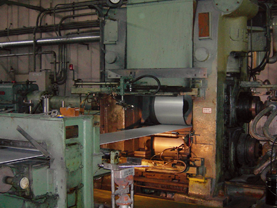
2連続鋳造
溶かしたアルミをノズルを通して直接冷却(水平)ロールに供給し、8~10mmの板を連続して作ります。
国内で初めての水平ロール式連続鋳造機を使って製品化に成功する
鋳造速度の高速化により生産性が向上し、品質の安定化も実現しました。
【鳥取マイスター】 高度熟練技能者のご紹介
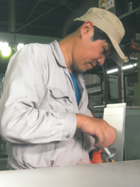
鋳造担当 須山喜文
国内初のアルミニウム水平ロール連続鋳造に22年前の試作段階から責任者として携わり、量産化のための品質規格、作業マニュアルを確立させ、国内で始めて薄板の鋳造母材の量産化に成功。
現在では技術や品質において世界でも優秀なアルミニウム展伸材を生産できるまでになった自社にとって、無くてはならない存在。海外のアルミニウムメーカーに赴き、連続鋳造技術について指導及びアドバイスを行っている。
現在世界的な新規素材のためのアルミニウム合金開発に責任者として従事している。
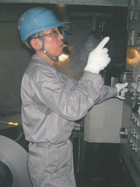
機械加工担当 高見 邦夫
国内でも数少ないアルミニウム板材メーカーの中で、自社の冷間圧延技術・製造ノウハウを独自に確立。
鋳造後、連続鋳造で製造された板材を最薄60μmに成形する作業に従事し、毎分600m以上の高速度で圧延中に、板形状や板緩み張り状態を瞬時に判断して圧延荷重、張力、速度、冷却水噴射位置の調整に高度な熟練技能を発揮。
管理職として、製品仕様や社内規格の決定など製造業務のほか、従業員の能力把握と育成計画策定などの管理部門業務にも携わり、後継者育成に貢献。

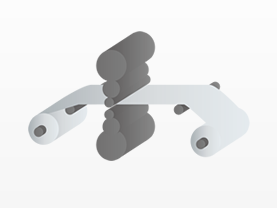
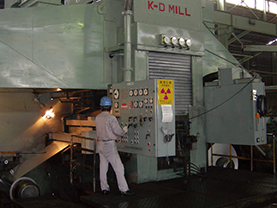
3冷間圧延
指定の厚みまで薄くして、強度確保、表面性状の作りこみをします。

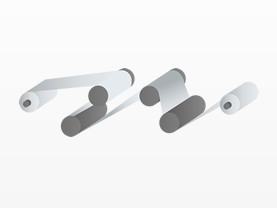
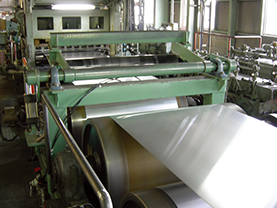
4テンションレベラーライン
圧延したアルミニウム板の歪みを矯正し、高精度に仕上げます。

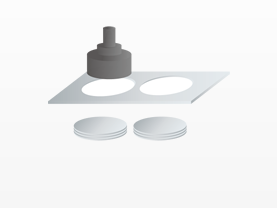
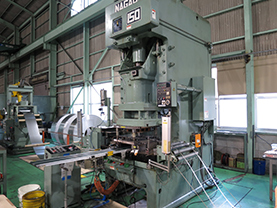
8プレス
コイルから色々なサイズの金型で丸板を抜き取ります。

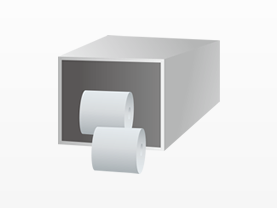
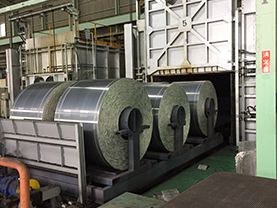
9焼鈍
焼鈍は材料の軟化と残留応力の除去のために行います。

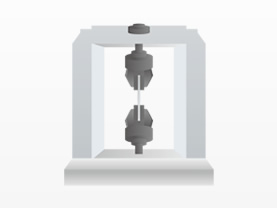
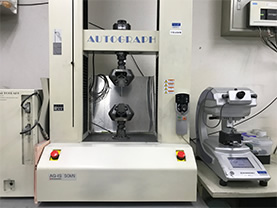
10検査
梱包前に寸法・機械的性質(材料強度)を計ります。

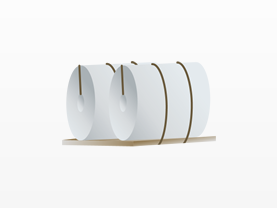
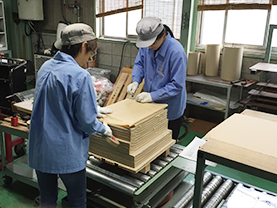
11梱包
完成した製品を検品・梱包し、出荷します。